Papers by Vadim Silberschmidt

Journal of The Mechanical Behavior of Biomedical Materials, Mar 1, 2021
Polydimethylsiloxane (PDMS) materials are widely adopted in the manufacture of facial prostheses,... more Polydimethylsiloxane (PDMS) materials are widely adopted in the manufacture of facial prostheses, lab-on-chip devices and scaffolds for soft-tissue engineering applications; however, their processing by additive manufacturing (AM) has proved challenging. Liquid silicone rubbers (LSRs) are favoured for their high shape fidelity when cast, but their low viscosity and surface tension often prevent self-support, post-extrusion. Poly(ether) ether ketone (PEEK) particle reinforcement through interfacial bonding has proven to enhance key properties of PDMS, expanding their end-use functionality. Still, the impact of such particles on the printability of LSR-PDMS is not explored. In this study, for the first time, solvent-free biocompatible PDMS-PEEK composites (up to 30 wt.% PEEK) were successfully characterised for material extrusion (ME) printing. Rheological analysis confirmed shearthinning of all PDMS-PEEK composites under applied load (within the tolerances of the printer) and dominant storage moduli at rest (i.e. prints can self-support), considered highly desirable for ME-based printing. Attained rheological datasets were used to guide initial printability studies, which revealed finer track fidelity with rising fractional content of PEEK, at comparable print speed and displacement values. Composites with higher PEEK content demonstrated significant increases in Shore A hardness and stiffness (in tension and compression) in bulk form. Last but not least, enhanced shape fidelity (thanks to PEEK reinforcement) and geometrical autonomy further expanded the manufacturing freedom of PDMS, whereby infill density could be controlled in order to increase the range of mechanical performance, previously unachievable with conventional casting fabrication. Fundamentally, this could lead to the manufacture of bespoke spatially graded multi-material structures and devices that could be used to replicate the heterogenous properties of soft human tissues and in other advanced material applications.

Journal of Manufacturing Processes, 2023
Machining of micro SiCp/AA2124 composites remains a challenge with conventional machining yieldin... more Machining of micro SiCp/AA2124 composites remains a challenge with conventional machining yielding poor surface quality with high tool wear. In this paper, we study two distinct and unique hybrid machining processes with the aim of improving the machining outcome of three types of micro-SiC/AA2124 composites with different particulate volume fractions and sizes. The class of composites studied is available commercially and is being used in industrial applications, thus assessing the machining outcomes becomes even more pertinent. Vibratory machining where the tool is made to vibrate at ultrasonic frequencies, known as ultrasonically assisted turning (UAT), is shown to yield some clear improvements in machining. Next, we incorporate laser assistance with the goal of inducing thermal softening in the process zone. This hybrid-hybrid machining process which is referred to as laser-ultrasonic-assisted turning (LUAT) has the potential for improved machining outcomes with significantly reduced machining forces and surface topology improvement. Our studies indicate that an optimum laser power exists for each type of metal matrix composite considering the particle size and volume fraction of the particulate reinforcements yielding benefits in terms of machining force reduction, surface topology improvement and potentially tool life enhancement. In addition, a computational machining model was developed which can be used to predict the machining outcomes with variable machining parameters.

Microelectronics Reliability, Apr 1, 2015
The lifetime of micro electro-thermo-mechanical actuators with complex electro-thermo-mechanical ... more The lifetime of micro electro-thermo-mechanical actuators with complex electro-thermo-mechanical coupling mechanisms can be decreased significantly due to unexpected failure events. Even more serious is the fact that various failures are tightly coupled due to micro-size and multi-physics effects. Interrelation between performance and potential failures should be established to predict reliability of actuators and improve their design. Thus, a multiphysics modeling approach is proposed to evaluate such interactive effects of failure mechanisms on actuators, where potential failures are pre-analyzed via FMMEA (Failure Modes, Mechanisms, and Effects Analysis) tool for guiding the electro-thermo-mechanical-reliability modeling process. Peak values of temperature, thermal stresses/strains and tip deflection are estimated as indicators for various failure modes and factors (e.g. residual stresses, thermal fatigue, electrical overstress, plastic deformation and parameter variations). Compared with analytical solutions and experimental data, the obtained simulation results were found suitable for coupled performance and reliability analysis of micro actuators and assessment of their design.

Composite Structures, Nov 1, 2018
Composites reinforced with braided textiles exhibit high structural stability and excellent damag... more Composites reinforced with braided textiles exhibit high structural stability and excellent damage tolerance, making them very attractive for defence, aerospace, automotive and energy industries. Considering the real-life service environment, it is crucial to study a dynamic response of a composite structure and its energy-dissipation ability, especially under repeated low-velocity impacts. So, a series of drop-weight tests were carried out followed by X-ray computed micro-tomography to characterize damage morphology of braided composite specimens. Meanwhile, a multi-scale computational approach was explored and implemented as a user-definedmaterial subroutine (VUMAT) for ABAQUS/Explicit to capture main damage modes of a braided textile composite, while its delamination was modelled by employing cohesive-zone elements. Load-and energy-time curves were obtained both experimentally and numerically. The predicted levels of peak forces and absorbed energy were found to agree with the experimental data. An extent of delamination and damage accumulation in the braided composite was predicted numerically and analysed; it was found that material responses to repeated impacts had two types depending on the level of normalised impact energy. The presented modelling capability could contribute to design of braided composite structures for various applications.

Journal of Materials Science, Aug 7, 2010
One of the most important characteristic features of a low-density thermally bonded nonwoven mate... more One of the most important characteristic features of a low-density thermally bonded nonwoven material is its discontinuous and non-uniform microstructure, resulting in a complicated and unstable deformation mechanism of the material. In order to estimate the effects of such microstructure on the overall mechanical properties of the non-woven material, tensile tests are carried out for specimens with different systems of marks for both two principle directions-machine direction and cross direction-with images being captured with high-speed camera. The non-uniform strain fields are analysed based on the obtained images. Discontinuous finite-element models are developed to study the deformation mechanism of nonwoven specimens in both principle directions, and the effects of the discontinuous and non-uniform fibrous network and different arrangements of bond points are analysed numerically.

Biomechanics and Modeling in Mechanobiology, Oct 25, 2022
Balloon pre-dilation is usually performed before implantation of a nitinol stent in a femoropopli... more Balloon pre-dilation is usually performed before implantation of a nitinol stent in a femoropopliteal artery in a case of severe blockage or calcified plaque. However, its effect on performance of the nitinol stent in a diseased femoropopliteal artery has not been studied yet. This study compares the outcomes of stenting with pre-dilation and without it by modelling the entire processes of stent deployment. Fatigue deformation of the implanted stent is also modelled under diastolic-systolic blood pressure, repetitive bending, torsion, axial compression and their combination. Reduced level of stress in the stent occurs after stenting with pre-dilation, but causing the increased damage in the media layer, i.e. the middle layer of the arterial wall. Generally, pre-dilation increases the risk of nitinol stent's fatigue failure. Additionally, the development of in-stent restenosis is predicted based on the stenting-induced tissue damage in the media layer, and no severe mechanical irritation is induced to the media layer by pre-dilation, stent deployment or fatigue loading.

Multiscale and Multidisciplinary Modeling, Experiments and Design, Jun 26, 2023
Superior mechanical and thermal properties, high wear resistance and a competitive price of compa... more Superior mechanical and thermal properties, high wear resistance and a competitive price of compacted graphite iron (CGI) have made it an integral part of industry worldwide. In its applications in automotive engines, high-temperature environments cause thermal expansion that can result in emergence of interfacial damage in CGI. Although graphite-matrix interfacial damage is considered the main damage mechanism that can lead to total fracture of CGI, extensive research on CGI has not yet fully investigated this phenomenon at the microscale, especially under pure thermal loading. This paper focuses on the high-temperature performance of CGI and the onset of damage in graphite in thermal cycles. Three-dimensional numerical models are developed, with a single graphite inclusion embedded in a unit cell of the metallic matrix. Elastoplastic behaviour is considered for both phases in simulations. The effects of morphology and orientation of graphite inclusions on a response of an entire unit cell to thermal loading are investigated. Also, the influence of periodic and fully-fixed boundary conditions on the damage behaviour of CGI is discussed. The results can give a better understanding of the fracture mechanisms of CGI exposed to elevated temperatures.
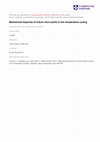
In this study, mechanical properties of indium micro-joints exposed to low temperature cycling we... more In this study, mechanical properties of indium micro-joints exposed to low temperature cycling were investigated. The metallization structure of Ni/Cu was specially used as a substrate to form indium joints for mechanical tests. This paper focuses mainly on the tensile test of indium joints at thermal cycling from 300 K to 77 K. The Young's modulus, the ultimate strength and yield strength of the material were obtained. The failure mode after different loading histories was analyzed. The results indicate the decline of the Young's modulus with the increase in the number of thermal cycles; however, the ultimate/yield strength of indium joints did not show an obvious trend with the number of thermal cycling. It was confirmed that indium joints still maintain a high ductility even after 20 thermal cycles. Finally, the associated modeling provides an insight predicting that an interface between indium and copper could be the potential site for failure in thermal cycling.

International Journal of Fracture, Jun 1, 2021
Double-cantilever beams (DCBs) are widely used to study mode-I fracture behavior and to measure m... more Double-cantilever beams (DCBs) are widely used to study mode-I fracture behavior and to measure mode-I fracture toughness under quasi-static loads. Recently, the authors have developed analytical solutions for DCBs under dynamic loads with consideration of structural vibration and wave propagation. There are two methods of beam-theory-based data reduction to determine the energy release rate: (i) using an effective built-in boundary condition at the crack tip, and (ii) employing an elastic foundation to model the uncracked interface of the DCB. In this letter, analytical corrections for a crack-tip rotation of DCBs under quasi-static and dynamic loads are presented, afforded by combining both these data-reduction methods and the authors' recent analytical solutions for each. Convenient and easy-to-use analytical corrections for DCB tests are obtained, which avoid the complexity and difficulty of the elastic foundation approach, and the need for multiple experimental measurements of DCB compliance and crack length. The corrections are, to the best

Journal of The Mechanical Behavior of Biomedical Materials, May 1, 2019
Functionally graded materials (FGMs), with varying spatial, chemical and mechanical gradients (co... more Functionally graded materials (FGMs), with varying spatial, chemical and mechanical gradients (continuous or stepwise), have the potential to mimic heterogenous properties found across biological tissues. They can prevent stress concentrations and retain healthy cellular functions. Here, we show for the first time the fabrication of polydimethylsiloxane and poly(ether) ether ketone (PDMS-PEEK) composites. These were successfully manufactured as a bulk material and functionally graded (stepwise) without the use of hazardous solvents or the need of additives. Chemical, irreversible adhesion between layers (for the FGMs) was achieved without the formation of hard, boundary interfaces. The mechanical properties of PDMS-PEEK FGMs are proven to be further tailorable across the entirety of the build volume, mimicking the transition from soft to harder tissues. The introduction of 20 wt.% PEEK particles into the PDMS matrix resulted in significant rises in the elastic modulus under tensile and compressive loading. Biological and thermal screenings suggested that these composites cause no adverse effects to human fibroblast cell lines and can retain physical state and mass at body temperature, which could make the composites suitable for a range of biomedical applications such as maxillofacial prosthetics, artificial blood vessels and articular cartilage replacement.
Materials Science and Engineering: C, May 1, 2016
Effect of microstructure on anomalous strain-rate-dependent behaviour of Effect of microstructure... more Effect of microstructure on anomalous strain-rate-dependent behaviour of Effect of microstructure on anomalous strain-rate-dependent behaviour of bacterial cellulose hydrogel bacterial cellulose hydrogel PLEASE CITE THE PUBLISHED VERSION
Polymer Testing, Jul 1, 2017
Failure analysis of plain woven glass/epoxy laminates: Comparison of off-Failure analysis of plai... more Failure analysis of plain woven glass/epoxy laminates: Comparison of off-Failure analysis of plain woven glass/epoxy laminates: Comparison of offaxis and biaxial tension loadings axis and biaxial tension loadings PLEASE CITE THE PUBLISHED VERSION

Advanced composites and hybrid materials, Jul 24, 2020
Additive manufacturing of composites offers a potential for a new level of control over a materia... more Additive manufacturing of composites offers a potential for a new level of control over a material's structure at the microscale. The focus of this work is a 2-hydroxyethyl methacrylate (HEMA)-based gelation system with orderly distributed carbon nanotubes (CNTs). CNTs undergo shear-induced alignment during printing process, and retain their orientation after the polymerisation of HEMA monomers, thereby, forming a nanocomposite with anisotropic mechanical and electrical properties. It is characterised with an intensive programme of mechanical tests including quasistatic uniaxial stretching, and dynamic cyclic loadings, as well as its four-terminal sensing of conductive characteristics. A coupling effect of mechanical and electrical properties is also studied. The experimental findings are discussed in detail and demonstrate that the orientation of CNTs affects both the mechanical and electrical conductive properties of the nanocomposites in terms of its ultimate strength, resistivity, and a piezoresistive coefficient. Understanding of anisotropic electromechanical properties of printed PHEMA-CNT hydrogel nanocomposite will ultimately underpin the development of smart soft materials for diverse applications, such as biomimetic nucleus pulposus or flexible electronics.
Delamination is one of the main failure mechanisms in bonded composite joints. Owing to a conside... more Delamination is one of the main failure mechanisms in bonded composite joints. Owing to a considerable spatial scatter in adhesion over the interface in such joints, initiation of a delamination zone and propagation of its front are highly random processes. The main delamination front is rather tortuous, and many small delamination spots are formed in its immediate vicinity. These processes can be additionally complicated in the case of loading types such as fatigue and/or multiple impacting. This paper deals with experimental methods of analysing delamination zones at various stages of their evolution. X-radiographs of delamination zones are digitalized and scaling analyses based on fractal and multifractal approaches are performed in order to quantify the morphology as well as the damage distribution in the immediate vicinity of delamination fronts.
Materials, Oct 7, 2022
This study describes the internal structure of materials used to produce medical stents. A two-le... more This study describes the internal structure of materials used to produce medical stents. A two-level elastoviscoplastic mathematical model, which sets the parameters and describes the processes at the grain level, was developed and numerically implemented. A separate study was conducted to identify the most dangerous deformation modes in the balloon-expandable stent placement using the finite-element method in COMSOL Multiphysics. As a result, the challenging strain state type required for setting the kinematic loading on a representative macrovolume in the two-level model was obtained. A yield surface for different deformation paths in the principal deformation space for stainless steel AISI 316L was obtained and the effect of grain size on the deformation behavior of this material was explored using the developed model.

Journal of The Mechanical Behavior of Biomedical Materials, Jun 1, 2021
Although biodegradable polymers were widely researched, this is the first study considering the e... more Although biodegradable polymers were widely researched, this is the first study considering the effect of combined testing environments and cyclic loading on the most important aspect related to additive manufacturing: the interfacial bond between deposited layers. Its results give confidence in applicability of the material extrusion additive manufacturing technology for biomedical fields, by demonstrating that the interface behaves in a manner similar to that of the bulk-polymer material. To do this, especially designed tensile specimens were used to analyse the degradation of 3D-printed polymers subjected to constant-amplitude and incremental cyclic loads when tested in air at room temperature (control) and submerged at 37 °C (close to in-vivo conditions). The mechanical properties of the interface between extruded filaments were compared against the bulk material, i.e. along filaments. In both cases, cyclic loading caused only a negligible detrimental effect compared to non-cyclic loading (less than 10% difference in ultimate tensile strength), demonstrating the suitability of using 3D-printed components in biomedical applications, usually exposed to cyclic loading. For cyclic tests with a constant loading amplitude, larger residual deformation (>100% greater) and energy dissipation (>15% greater) were found when testing submerged in solution at 37 °C as opposed to in laboratory conditions (air at room temperature), as used by many studies. This difference may be due to plasticisation effects of water and temperature. For cyclic tests with incrementally increasing loading amplitudes, the vast majority of energy dissipation happened in the last two cycles prior to failure, when the polymer approached the yield point. The results demonstrate the importance of using an appropriate methodology for biomedical applications; otherwise, mechanical properties may be overestimated.

Engineering Fracture Mechanics, Feb 1, 2020
Assessment of the energy release rate (ERR) of layered material structures with account for dynam... more Assessment of the energy release rate (ERR) of layered material structures with account for dynamic and vibration effects is important for understanding and predicting fracture behavior in various engineering applications. In this work, the pure-mode-I interfacial fracture behavior of a symmetric double cantilever beam (DCB) under constant-rate opening displacement is studied using a dynamics and vibration analysis of Euler-Bernoulli beams, and the ERR is derived. Furthermore, a 'dynamic factor' that quantifies the dynamic effect in relation to the static component of ERR is defined. The resulting expressions are relatively short, mathematically elegant and convenient-to-use by engineers and researchers, which increases their usefulness. It is found that the dynamic factor is a function of the characteristic time only, and that this is an intrinsic property of DCB structures. An approximate method is also proposed to predict the crack extension. Predictions of ERR and crack extension are in good agreement with results from numerical results with finite-element method (FEM) simulations. Using only the first vibration mode is sufficient to capture the amplitude and frequency of ERR variation predicted by the FEM. Using higher-order vibration modes causes divergence in the amplitude of ERR oscillation; this is due to the limitation of Euler-Bernoulli beams in vibration analysis.

Journal of Materials Engineering and Performance, 2021
This paper focuses on microstructural and mechanical characterization of metallic thin-walled tub... more This paper focuses on microstructural and mechanical characterization of metallic thin-walled tube produced with additive manufacturing (AM), as a promising alternative technique for the manufacturing of tubes as a feedstock for stents micromachining. Tubes, with a wall thickness of 500 lm, were made of 316L stainless steel using selective laser melting. Its surface roughness, constituting phases, underlying microstructures and chemical composition were analyzed. The dependence of hardness and elastic modulus on the crystallographic orientation were investigated using electron backscatter diffraction and nanoindentation. Spherical nanoindentation was performed to extract the indentation stress-strain curve from the load-displacement data. The obtained results were compared with those for a commercial 316L stainless steel stent. Both tube and commercial stent samples were fully austenitic, and the as-fabricated surface finish for the tube was much rougher than the stent. Microstructural characterization revealed that the tube had a columnar and coarse grain microstructure, compared to equiaxed grains in the commercial stent. Berkovich nanoindentation suggested an effect for the grain orientation on the hardness and YoungÕs modulus. The stress-strain curves and the indentation yield strength for the tube and stent were similar. The work is an important step toward AM of patient-specific stents.

Journal of The Mechanical Behavior of Biomedical Materials, Jun 1, 2016
Biological hydrogels, e.g. bacterial cellulose (BC) hydrogel, attracted increasing interest in re... more Biological hydrogels, e.g. bacterial cellulose (BC) hydrogel, attracted increasing interest in recent decades since they show a good potential for biomedical engineering as replacements of real tissues thanks mainly to their good biocompatibility and fibrous structure. To select potential candidates for such applications, a comprehensive understanding of their performance under application-relevant conditions is needed. Most hydrogels demonstrate time-dependent behaviour due to the contribution of their liquid phase and reorientation of fibres in a process of their deformation. To quantify such time-dependent behaviour is crucial due to their exposure to complicated loading conditions in body environment. Some hydrogel-based biomaterials with a multi-layered fibrous structure demonstrate a promise as artificial skin and blood vessels. To

Journal of Manufacturing Processes, Feb 1, 2021
Vibration-assisted cutting (VAC), a promising technique, proved to enhance the machinability of d... more Vibration-assisted cutting (VAC), a promising technique, proved to enhance the machinability of difficult-to-cut materials. Its significant superiority with regard to conventional cutting (CC) is considered to be closely related to variation of a shear angle in the primary shear zone and specific frictional behaviour at tool-chip interface. This paper analyses kinematics of VAC, focusing on critical stages of tool-workpiece interaction. Based on the evolution of kinematic parameters, a transient shear angle and a tool-chip contact length are investigated in a cycle according to these stages. To predict the transient parameters, an analytical model of the cutting process is proposed based on non-equidistant shear-zone and tool-chip sliding-sticking zone theories. This model for VAC can not only predict the dominant parameters of the cutting process (e.g., cutting force, friction coefficient), but also the secondary ones (e.g., shear strain). Experimental validation of the developed model is performed with orthogonal VAC of titanium alloy, and the shear angles are measured with optical microscopy of chip samples. For various process parameters, the effective shear angle in VAC is larger than that in CC. However, the average shear angle in VAC is smaller than the shear angle in CC. The proposed model can not only effectively predict the shear angle and frictional behaviour in VAC, but also other process parameters in a vibration cycle, enriching the theory of the VAC process.
Uploads
Papers by Vadim Silberschmidt